Why is the Toyota production system (TPS) difficult to understand?
- hidet77
- Nov 4, 2021
- 3 min read
Updated: Nov 9, 2021
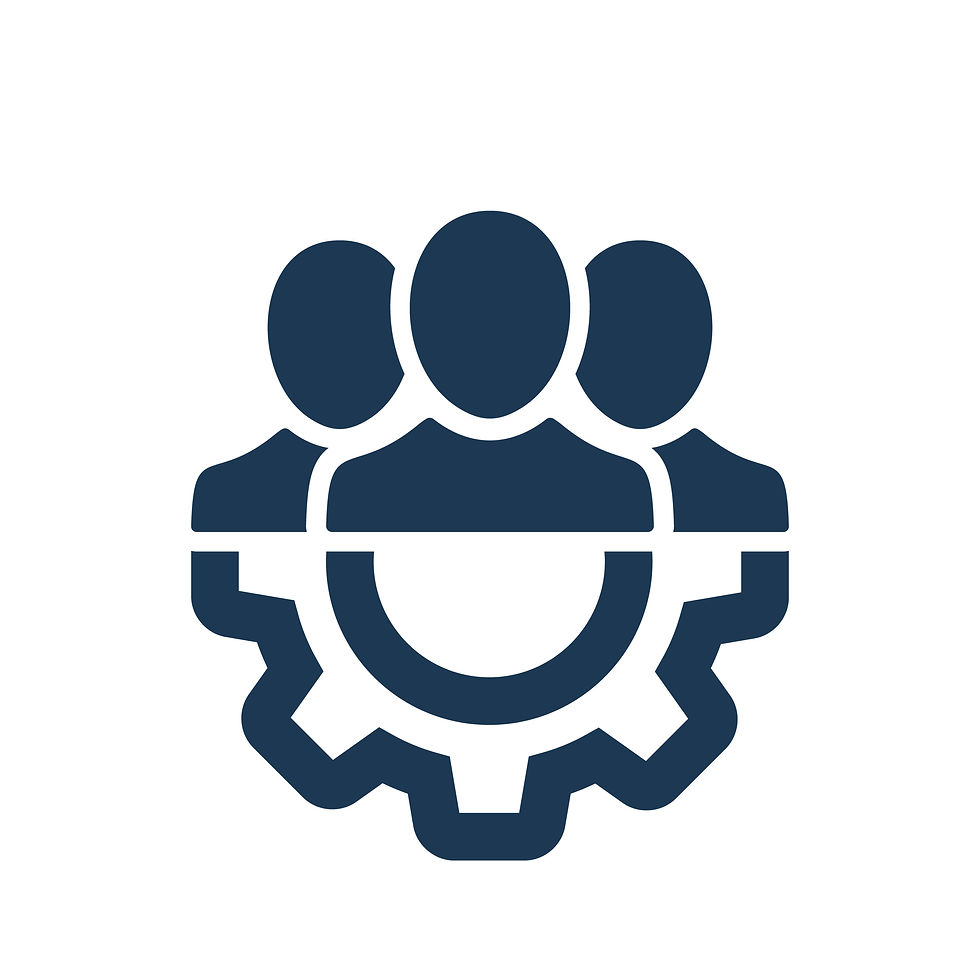
Why is the Toyota production system (TPS) difficult to understand?
Our root cause analysis reached Frederick Winslow Taylor’s “Scientific management.”
Taylor’s “Scientific management” is the starting point of modern management. One of the vital aspects of his thinking is “Functional Organization.” Even today, there are many organizational theories, but those evolved from the functional organization. When many leaders and managers encounter TPS/Lean, they immediately create the office. Some companies have multiple offices of lean, continuous improvement, alphabet PS, etc. But we must ask this question, “Is TPS a function?”
“Quality.” An essential aspect of business that Deming discovered. It was missing in Taylor and its followers’ work. So after discovery, quality became a function. But the quality was never an independent function. Product & process engineering needs to support this thinking fully. The operation needs to respect quality. Is there any function that is not related to quality? None. This thinking leads to the concept of “Total quality management.” Unfortunately, in many cases, TQM means just printing many posters that say, “Quality is everybody’s responsibility.” But still, those slogans do touch the truth that quality is in every work. In many ways, TPS/Lean is following its big sibling’s footsteps. TPS is not an independent function. Continuous improvement is everyone’s responsibility. Flow is something that everyone should be aware of in this cash flow-centric business world. And the siblings continue to like “innovation,” “environment,” “development,” etc. To some degree, should “finance,” “HR,” and “strategy” be kept as a separate or independent function? When Taylor suggested such a functional organization, there were only a few functions. Today, the inflation in the number of functions continues. Yet, none of the functions is fully independent, asking more time for coordination with existing ones. None of the functions is magic. Just because there is an office does not solve any problems.
One big reason why TPS is difficult to understand is that it integrates functions. Quality is a perfect example. Jidou-ka concept incorporated quality into every standardized work. The Just-in-time system stops if there is a quality problem. For example, one of the main rules of Kanban is to have 100% good parts. Kanban shouldn’t be calculated for X% of defects. Every concept has some quality connections.
One interesting thing that TPS integrated is management and industrial engineering. Taylor is known as the father of scientific management. But he is also the father of industrial engineering. Why did his followers decide to live in two separate worlds? Has anyone investigated the pros and cons of separating these two subjects? To some degree, it is a tragedy that these two siblings only communicate based on ROI. When the Japanese translated “industrial engineering,” they translated it as “managerial engineering.” I do not know if this was intentional or not, but this mistake represents what TPS is. TPS continuously integrates management and engineering. The manager might know a little about the technology. But they will go to the shop floor and ask the engineer, “it looks like this process has room to improve?”
Why is a functional organization not working? There are many pros and cons. I think this is the perfect case of “Prisoners’ dilemma.” When two prisoners are in cells and make decisions, even though corporations lead to maximum benefits of both, they choose an option that looks optimum individually, leading to catastrophe for both. Some will argue that operations can help each other because we can have meetings to share information. Unfortunately, individual KPIs will drive the organizations in many directions. Also, the more functions you have, the more time it takes to come to a consensus. By the time an agreement is reached, the conditions have shifted. We are the “prisoners” of functions. In many ways, TPS hates these “prisoners” condition. At the process level, TPS implements continuous flow instead of isolated islands. They design customer-focus lines instead of job shops. One key to understanding the game theory is the “enforceable agreement.” TPS accomplishes that by creating the process, which they have to follow the standards. They also use job rotation to have managers experience other functions. For example, my coach was responsible for the quality, international supply chain, and TPS at one point in a small factory. Besides, all these functions have some root in Taylor. Why can’t we, with the help of advances in science, manage these functions together?
After all, science is about decomposition and integration. So thank Taylor for starting the decomposition of management into functions. We need to integrate, and that is TPS.
Comments