Why is OEE not necessary TPS?
- hidet77
- Feb 4, 2022
- 6 min read
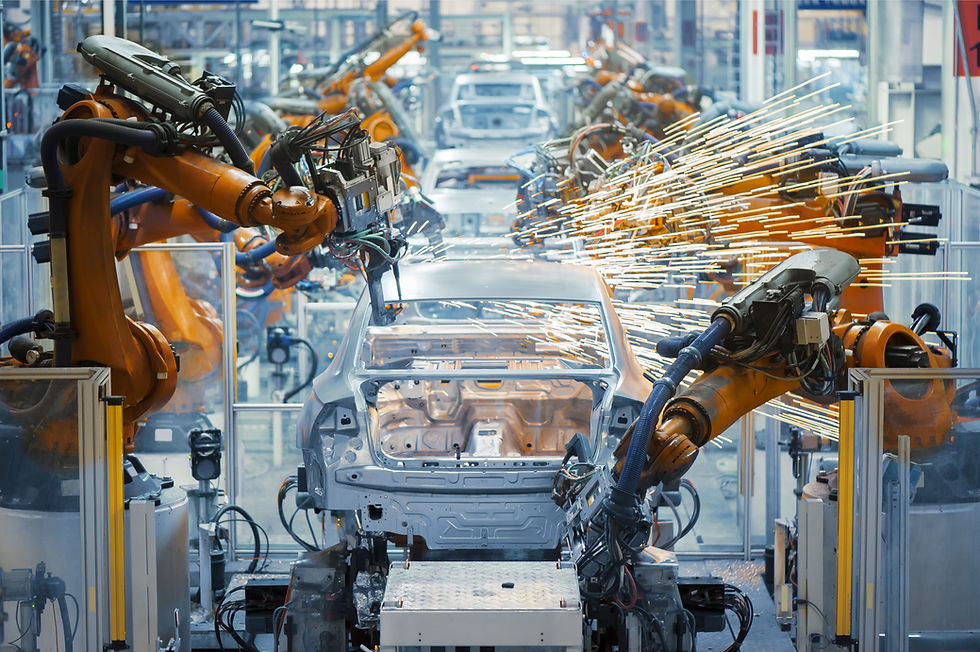
Japan Institute of Plant Maintenance (JIPM) and Seiichi Nakajima developed Overall equipment efficiency (OEE) in total productive maintenance (TPM).
TPM and TPS have a similar backgrounds. As JIPM states, the initial TPM started in Denso, a Toyota group supplier.
But that doesn’t mean OEE is TPS.
And OEE contradicts TPS in many ways.
1. Why do we need to separate the “P” & “Q”?
2. Just In Time > Efficiency. Aka, don’t overproduce.
4. Just chasing OEE is not TPM
Why do we need to separate the “P” & “Q”?
Ohno’s book, “Workplace management,” explains this “Kadouritsu (可動率)” as “Operational availability.” Operational availability is “the rate (率) you can(可) run (動) the machine.” If you have 8 hours shift and the machine was down for one hour, your OA will be 87.5%. Very simple.
The OEE includes this availability inside its equation. OEE = Availability(A) X Performance(P) X Quality(Q). We have this bias that we think the more is better. So this equation looks more intelligent. But let’s take a deep dive.
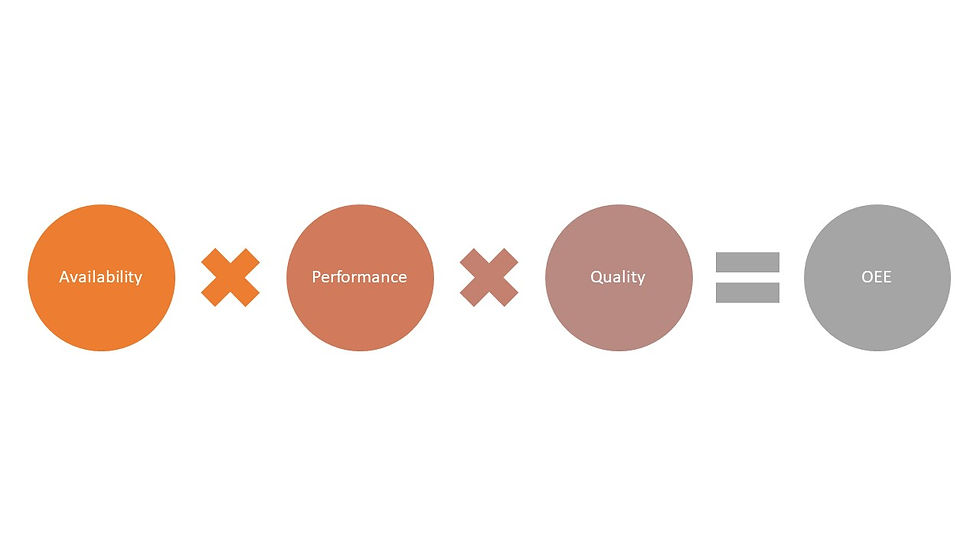
What is performance? It compares the machine’s actual speed against the designed speed. But why do we need to compare these two? Is it allowed to run below the designed rate? Think of this from the standardized work. I have a machine that does not always run at the designed speed. Can I create excellent standardized work for the worker, where a machine sometimes runs below (or above) the designed rate? Suppose 60 seconds is the machine’s cycle time. An operator arrives at its workstation and finds out the machine’s performance is 90%, running at 66 seconds. Should we re-balance the standardized work considering 66 seconds? Should we keep some allowances between the machine and the operator so that machine performance can fluctuate? All of these actions and thinking are protecting the waste. Just implement a simple rule. Do not accept machine performance different from 100%. If the performance fluctuates, stop and fix the problem.
Thinking regards to quality is similar. What I think is essential is this 100% or 0 thinking. In between is the old traditional thinking where “as long as we can make the output, it’s ok.” TPS calls this thinking “Mura.” And TPS wants to eliminate such fluctuations.
Here is a very hypothetical story I made to explain this OEE thinking.
Suppose you walk into your beloved office and find the following note on your desk.
“Hi, this is the IT group. Your computer and the network are 10% slower than expected. This happens. Also, 10% of the data you make or send will convert into defects. Please don’t ask us why. But the good news is that both your PC & network is “available” all day. It is above “world-class.” Deal with it. Love, IT”
I hope the IT group will survive the day.
But this is the same message that we are sending to the shop floor. Where is “respect for people”? The bottom line is that both “P” and “Q” need to be 100%. I am still researching the original reason why they separated the “A,” “P,” and “Q.” However, if they wanted to say that any performance & quality issue below 100% is a crisis and highlight those issues because it is completely unacceptable, it makes sense. Unfortunately, that is not the way how we treat performance & quality. Many are making poor compromises, creating chaos on the shop floor.
The truth is that most maintenance accepts this challenge to keep the performance and quality at 100%. I really appreciate this kind of maintenance work and commitment. But the resistance comes from management, especially those who don’t come to the shop floor.
2. Just In Time > Efficiency. Aka, don’t overproduce.
The second “Kadouritsu” is translated as “Rate of operation” in the “Workplace management,” which I might say is the trickiest translation in this book.
Typically, “Rate of operations” is used as the ratio of output divided by capacity. The easiest way to improve the rate of operations traditionally is to increase the output. Traditional accounting will count any output as the same inventory. “Economy of scale” justified this thinking.
The trick here is that Ohno and TPS state that the output must match the demand in a just-in-time way. The most significant waste is “over-production,” which is any volume more than the market. And they are not just talking about volume, but also about the mix in a levelized way. The operations need to accomplish the levelized market by following the exact one-by-one sequence. This Kadouritsu is about what is the ratio(率) of your work(働)earning(稼)? If anything, I might call this a “Just-In-time” rate, which represents your operations system’s match against the market.
The difficulty of this “Just-In-Time” rate is almost impossible to measure. Is following the levelization always good? Should I ignore confirmed orders above levelized volume? But if I always prioritize the actual orders too much, I will destroy the levelization, simply firefighting orders every day.

And this is a big problem of OEE. The large batch will favor OEE. Over-production raises the OEE. OEE can ignore the Just-In-Time principle and hurt the business. The operations have produced products efficiently, but the market didn’t need them. I think that Ohno’s definition of “Productivity” is “Effectiveness” X “Efficiency,” which efficiency without effectiveness to the market has no meaning. Running the machine efficiently doesn't necessarily mean you produced a value effectively.
3. What is the point of measuring efficiency with lots of waste?
When I write “Kadouritsu,” there is confusion on the second symbol, is it 働 or 動? This discussion happens in the “Jidouka” concept. 自動化 means automation. 自働化means autonomation. 動 represent “movement,” while 働 represent “work.” So when I write 稼動率, this means the rate(率) of earning(稼) movements(動)or ratio of value-adding work in the movement.
This value-add work ratio is another problem of OEE. As I have mentioned in my previous post, we can have a process that is 100% waste and call it a “bottleneck” and chase OEE. Even if 100% is an overstatement, can we compare a machine that has 20% waste and 80% waste on OEE?
Suppose the shop floor improved the process by eliminating the waste. The factory accomplished a 10% reduction in machine cycle time. If the factory’s output increases by 10%, the OEE remains the same. If the rise in output is below 10%, the OEE should go down. As I mentioned in my last post, the baseline capacity often does not change quickly in an environment that focuses too much on OEE. In such an environment, an effort to improve output that doesn’t improve the OEE looks like a “waste.”
Focusing on the ratio of value-add work could also stop Kaizen. In theory, the ratio of value-adding work should get higher as we do Kaizen. But then, what happens if we discover that what we defined as value-add work had some hidden waste? Such discovery could reduce the ratio by converting the value-add work as waste. There is a good motivation for the management to ask this question. They want to know if they need to invest or rely on Kaizen for a future volume. They might have good intentions, but they might have a reverse impact on the learning process.
After all, Ohno questions “arithmetic calculations.” Any calculations will have blind spots. OEE or any ratio has many blind spots. These KPIs don’t replace the management going to the shop floor.
4. TPM
OEE came from Total Productive Maintenance (TPM). What is TPM? TPM states that we should understand the science of machine breakdown. By understanding this science, we can predict the problem, and therefore we can prevent it. We can make this work more productive once we design scientific maintenance that prevents unplanned downtimes. By applying this science, OEE should improve. This premise of OEE has disappeared. Most chase the OEE numbers without understanding the logic of maintenance activity. More likely, there is no logic or just pushing, like maintenance determining the frequency of work based on available resources. Where is the science behind this “OEE 85% is world-class”? Is 15% unplanned downtime the same as 15% planned downtime? After all, good TPM should provide predictable output. Simply hitting a higher OEE number has no meaning. The valid TPM is when we learn the science behind the number to guarantee a higher availability for the future.
After all, OEE is just a number. This doesn’t replace the need for management to be on the shop floor.
Comments