Try Heijyunka on a smaller scale.
- hidet77
- Mar 17
- 3 min read
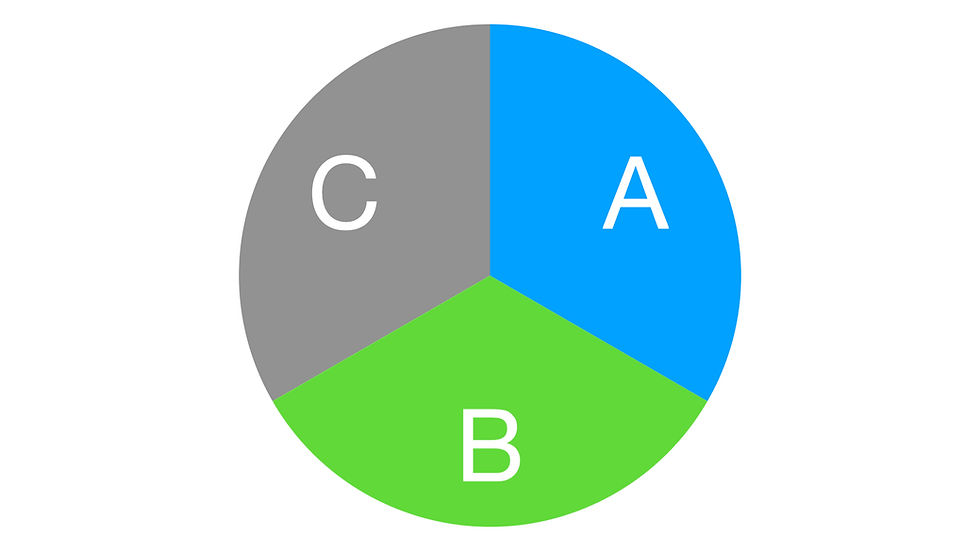
Heijyunka (Levelization) is considered the foundation of the Toyota Production System. Despite its importance, very few have challenged this concept. Many think that this is complex due to the product mix and customers. Factories will have thousands and more types of products, and it is almost impossible to Heijyunka.
Question: do we need to be perfect from day one?
Don’t try to be perfect. Start with incremental steps.
1️⃣ Level the apparent high work contents product
One of the production lines had a particular product that had double the amount of work. (The name of the product was double XXX) The production line hated this monster. So, they procrastinated. They delayed running these products until the sales side got upset. Because of this procrastination, orders accumulate. The production needs to be in batches at the end of the week or month. Output stumbles. Anger everywhere.
So, we only leveled these doubles. We agreed with the sales on how much of the volume should be these products. It turned out to be 20%. So we decided that every fifth unit would be that double product. We guaranteed the production that they will always have four regular units after a double. In other words, production should expect the double to come on every fifth unit. It was elementary, but this worked. We did some Kaizen on the work contents of the double, but the main change was how we flow the product with high work contents.
In today’s world, we have many product variations. Instead of leveling everything, start with those that production knows cause some fluctuations. If you have multiple types of concern products, try introducing them into Heijyunka condition one by one. Too often, complexity is used as an excuse to do nothing. Many places use the complex unit to cause the below target volume without any evidence. Doing nothing is worse than trying to Heijyunka. Start with the big “Monsters.” You don’t have to be perfect.
2️⃣ Level the destination
Many processes supply to multiple customer processes.
A machine had three customer processes. Every day, the area was chaotic with customer orders. The original thought was that they would produce in large batches so that the large inventory would keep the customers running without interfering with the machine. They even built a warehouse for this purpose. But these actions never worked. We investigated a material shortage in one customer process. Although the process was working hard to meet all customers' demands, and they believed they were responding, there were gaps in the schedule, causing shortages. We needed a guide to make sure we supply to all customers.
We implemented a simple mechanism for producing one by one to each customer. The first will be customer A, then B, C, and return to A. Since the machine could produce one by one, we only had to implement levelization. The impact was immediately noticed by the team leader, who handled the day-to-day chaos of customer orders. He stated that this “calmed” the process. He didn’t have to deal with shortages and angry calls from the customer processes. The machine refilled the orders in the Heijyunka way, and the panic disappeared. What’s more, the buy-in from this team leader sponsored execution. He constantly explained to the workers the importance of following the Heijyunka rules.
The rule applies the same when you have multiple suppliers. We should pull in the Heijyunka way and have a simple mechanism to control this. Otherwise, the bull-whip effect will kill the supplier.
We should reduce the batch sizes in both product and destination cases. The benefit of Heijyunka might not be captured when we produce in large batch sizes. But again, this is not another excuse not to start Heijyunka.
Heijyunka is not a perfect system. Like anything else in the Toyota Production System, it is subject to kaizen. What we need is the journey to better performance and the initial step. That initial step should be understanding the problems on the Genba. What kind of variance in products are the workers suffering? Which customers are we suffering to respond to? The people on the frontline know this. Instead of letting them figure out and suffer, Heijyunka is a way to provide a guide. Also, as demand, product mix, and customer changes, we should review the Heijyunka to ensure we offer the correct method to respond to the demand. In most cases, I start with simple pieces of paper with handwritten orders to be produced. This might look silly initially, but it has a powerful impact.
Again, start with something simple to implement the Heijyunka. Don’t let perfectionists bother you. Start with problems that people are suffering on the Genba. Simple Heijyunka helps when there are many products and destinations. And then, keep doing Kaizen on Heijyunka.
Comentarios