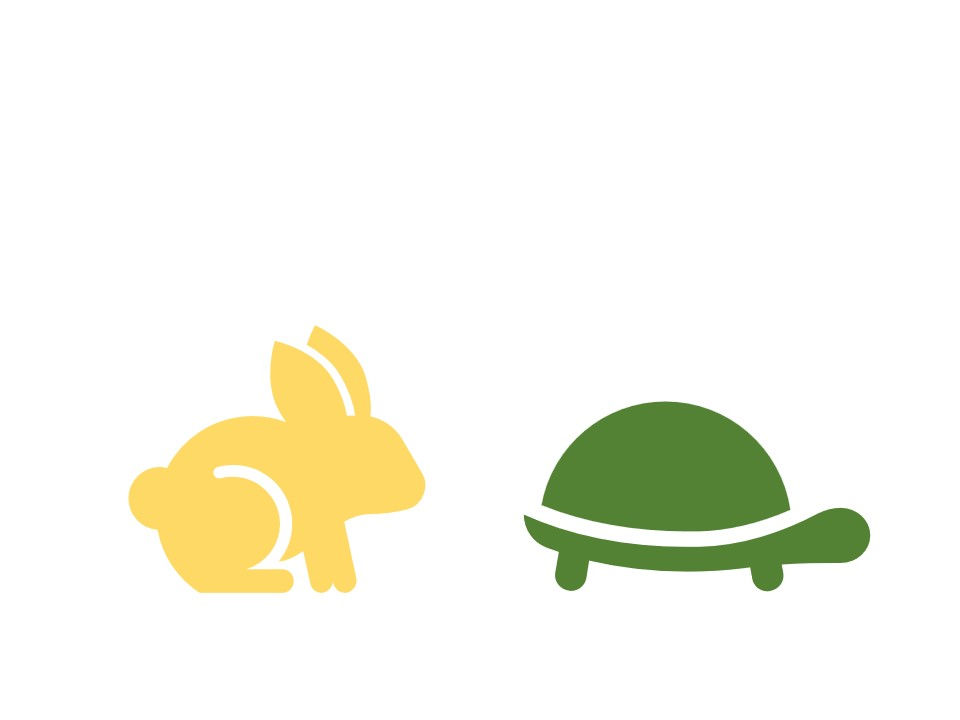
I ran into this factory version of the Tortoise and the Hare. The highly skilled operator took breaks so frequently that the operator was underperforming than the rest.
The factory management was eager to hire “high-skilled operators.” Yet, the result was a pity. Why? The management did not change the standardized work and Kaizen according to the high skills.
Standardized work must reflect the high skill levels and Kaizen accordingly. Otherwise, the high skills create waste. The Tortoise or the Hare is not the issue. It is the standard and management that do not change.
When I arrived at this factory, the plant manager informed me they had hired a new high skilled operator. I was puzzled by this decision but went to the shop floor with the manager. The operator was missing. The performance of the line was terrible.
“Oh, you haven’t updated your standardized work.” I pointed it out to the plant manager. He looked confused.
“What’s wrong with having the (high-skill) operator work with the current standard?”
“He will wait. Waiting is a waste. That’s why he’s disappearing.”
“Then he can pile up inventory.”
“That is over-production. The worst waste.”
I tried to understand the plant manager’s thinking. We all say we need high-skill operators, but the reason is different. His logic was similar to safety stock or insurance. The higher skill level will cover the problems and variations. He and the factory were not thinking about making any improvements.
At the same time, the new guy was frustrated. Why do I need to pace with the slow guys? And, as his frustrations piled up, he was isolated. The isolation leads to unacceptable behavior of leaving the line frequently. In the long term, such behavior will become toxic culture.
What “high skills” means are different. And, how someone wants to use the high skill is different. There was a plant with a maintenance guru. After the machine breakdown, the guru came and somehow fixed the issue. But we found something different. There were fewer mechanical troubles in the same plant with similar machines in another area. The reason was that the responsible maintenance of that area was doing preventive maintenance. Which skill is vital for the plant? Unfortunately, the guy who fixes the crisis looks “cooler” than the guy who constantly works to prevent a problem. Yet, it might not be the right skill for the organization’s success.
Two things are essential for high skill to be successful. Those are standardized work and Kaizen.
Having standardized work will help identify the high skills. The standardized work will quantify the impact of high skills and change the balance. Without standardized work, the high-skill operators have to waste on waiting or overproduce. These wastes will lead to frustrations. Do not try to force a high-skilled person into an old standard. We need standardized work to accept the high skill into our system.
Kaizen is also important. Having a new skill is like coming up with new ideas. It might be a small thing. Very small, and you might think that it is not important. Unless we constantly search for small ideas, we ignore the high skills. An environment where they respect small improvement ideas pays excellent attention to skills. Also, most high-skill won’t flourish with just skills alone. With standardized work, high skills will require changes in layout, material & tools presentations. Unless the factory is used to making such Kaizen, we will kill a high-skill.
Many companies focus on collecting high-skilled people without implementing standardized work and Kaizen. As a result, high skills do not necessarily lead to the business’s success. Start with standardized work & Kaizen. This will create an environment where high skills will be respected. And high skill people will be developed internally, not externally.
Comments