Takt Time
- hidet77
- Nov 21, 2023
- 4 min read
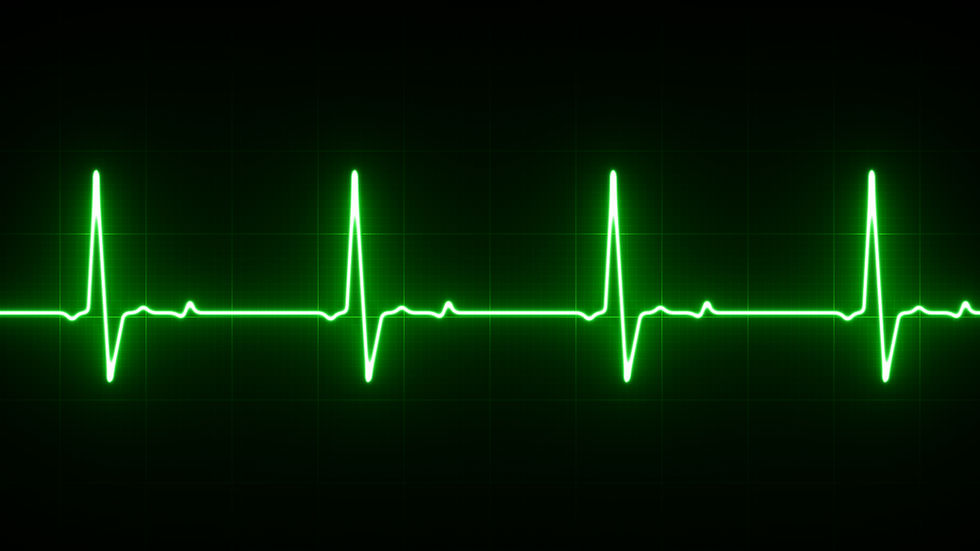
Whatever the origin of this concept, Toyota converted this concept to represent customer demand. By dividing total available time by the necessary quantity, takt time represents the time each unit should take at each standardized work.
But it is not just a calculation method. It’s not just a data collection frequency.
Takt time is the pulse of action inside the organization.
So don’t just calculate and collect data and be satisfied with those. Implementing takt time means to keep the organization alive with that concept.
“Takt” is a German word. Probably through Mitsubishi Heavy Industries in the Nagoya plant, located within Taiichi Ohno's commute to his college and life. However, when implemented inside the Toyota Production System, it represents the customer demand in time. There is this saying that time is a shadow of motion. And motions form the work. Therefore, we can convert work into time and balance the work to customer demand in time. Whenever there is a change in the demand, we should change the work balance. And, takt time played an important role.
The calculation is favored since it is simple. Yet, some have started to fake the takt time.
One of such is discounted “available time.” I have run into a place where they say the OEE should be 80%, so they multiply discounted available time by 20%. Some have excluded some time since they are struggling with start-ups. These are typical in places where they think that calculations are problem-solving without looking into the root causes. For them, takt time is another thing to calculate disrespecting the philosophy.
Another fake is the inflated demand. I encountered situations where sales, planning, engineering, and operations inflated demand. Each function might think they have only inflated “few” percentages, like 20%, but the total gap is enormous. Each function might think they have done their work, but the cost will be extremely high. It’s common to find such situations inside broken and poorly coordinated organizations.
These fake activities raise another question. Should we have different takt times inside a plant? In theory, creating a flow and rebalancing is possible when more processes have the same takt time. That should be the ideal. But it is challenging. However, should we have the same available time inside a plant? This should be possible (some technologies will not allow the same takt time.). Generally, those processes with different available times should be highlighted from the design stages. Differences in available time require inventories to adjust, which requires careful planning. Managers should be aware that there aren’t many takt time calculations. Most of my coaches will hear a takt time and automatically get a rough annual volume. That’s because the available time is almost fixed, and there are no other variables than volume.
What is more critical about takt time beyond its number or calculation is that there is an action at every takt time.
The obvious action is the action of the operators. Every takt time, the operator will start its standardized work. The standardized work should be balanced toward takt time. Every operator should start and stop at the same time. The standardized work will use components and release the Kanban. If not completed, the Andon must be pulled.
This Andon is the critical connection between the operator and the team leader. At every takt time, the team leader must ensure that no one within the team is delayed. If any, the team leader must go and help. This means that the processes the team leaders are responsible for must be visible to each other. If there are blind spots, the team leader cannot see the struggling process.
Another important thing is that the process needs to be “help-able.” There are many situations where the team leader does come to help. Yet, while the team leader helps, the operator watches. Although sometimes it is vital to see the correct method, it is also questionable. Yes, it is like a substitution in sports where you exchange a fresh player. But there’s no guarantee that the process will catch up. Instead, the operator and the team leader should become double manpower to boost performance temporarily. This way, the team can catch up to takt time.
The action of an organization to takt time doesn’t end at the team leader level. The higher management level should know operators should follow the standardized work at takt time. This looks like an orchestra; the music starts and ends when the conductor swings the takt stick (I heard this was why Toyota liked the word Takt.). They should also know that the team leaders should be helping at every takt time. If the team leaders are pulled frequently, then the higher level (Group leader) should come and help. Such frequent or significant problems should be quickly escalated so that higher managers can take proper action. The senior management should know that takt time is like the heartbeat of animals. Something should happen at every heartbeat. If not, then your organization is dead.
Once again, takt time is not just a calculation. It’s not data collection frequency. It is not just for the operators. It’s the heartbeat of actions among the organization that keeps them alive.
Comments