Taiichi Ohno and Maintenance
- hidet77
- Apr 9
- 3 min read
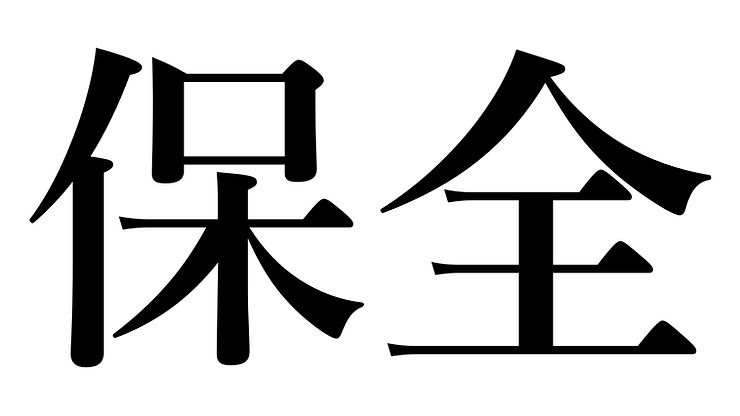
Seiichii Nakajima, pioneer of TPM, shared his experience with Taichi Ohno. Their relationship started when Toyota was awarded the Preventative Maintenance awards in the mid-sixties. Nakajima shared that they played golf and mah‐jongg together.
One of the interesting episodes was when Ohno started his career in the maintenance group. Ohno joined Toyota Boshoku in 1932, and his first assignment was in maintenance. Since Ohno’s background is in mechanical engineering, this makes sense. Also, Toyota was originally a manufacturer of auto-looms, meaning this maintenance could have access to the equipment designers. Ohno’s career looks like it started in maintenance, was introduced in standard work in the late thirties, transferred to Toyota Motor in 1943, and began the TPS around 1950. I doubt that TPS would be possible without the maintenance experience.
Ohno shared his thoughts on maintenance with Nakajima and the Japan Institute of Plant Maintenance (JIPM).
In Japanese, maintenance is “Hozen【保全】.” Ohno read as “全きを保つ.” [Subeki-wo-Tamotu.]
This symbol 【全】 means everything. It also means in perfect condition, safe, and scratch-free. The upper part of the symbol represents the entrance or the house. The bottom part originally shaped the “craft.” So, the original meaning was “all craft tools inside a case.” I will not say in 5S condition, but something very close.
The other symbol 【保】 means to guarantee. It also means to sustain and protect. The left side of the symbol represents a human. The right side is the shape of carrying a child. Because of this origin, this symbol is used a lot in healthcare. It means to take care like taking care of a baby. For example, the word “Hozen” was used in the following way in ancient China: In the Books of Han. “During the pregnancy, we need someone who can “Hozen” for the queen.” Because this symbol is close to maintenance, in railways, the maintenance of the track as Hosen 【保線】, a maintenance activity that existed before maintenance in factories in Japan.
Therefore, a Hozen means taking care of everything in good condition.
From here, Ohno has added wisdom in two ways.
First, based on his definition of Hozen, he challenged Nakajima that the word “preventative maintenance” is repeating the same meaning. Maintenance is about preventing; therefore, it doesn’t make sense. I initially thought this was only applicable to Eastern languages. However, as I understood the nuances of English “maintenance,” I realized that this includes “sustaining good conditions.” Maintenance included preventative aspects in many languages. If so, Ohno’s challenge is that the fact that we have to use “preventative maintenance” is an abnormal condition inside our mindset. Nakajima mentioned this episode, and he just accepted this challenge, although no action was taken.
The other piece of wisdom is that Ohno said that Hozen is about keeping everything in production in good condition. In other words, Ohno did not limit the scope of maintenance to equipment but to broader production topics. Since this statement was made at a conference of the Japan Institute of Plant Maintenance (JIPM), one of the original members of the JIPM, Yoshikazu Takahashi, summarized it in the following way. “By reducing work-in-process stock and creating a system of producing only what is necessary, when is necessary at the necessary quantity, the Toyota Production System raises the necessity of good maintenance system.” Takahashi refocuses that Ohno’s expectations on maintenance are to keep 100% operational availability and nothing below that. Many focus on just-in-time inventory reduction, but few focus on the need for good maintenance.
This resonates well with implementing a “Good” just-in-time system, which is not just about inventory reduction. It is about creating a need to improve the maintenance system. I have seen many maintenance managers freak out when we designed a system. But then, if we leave them alone, they will become resistant. Instead, by working together, we create a better maintenance system. Many talk about the importance of operators' autonomous maintenance. But just talking to them does create the need to fulfill such tasks. Instead, creating a system that promotes a sense of urgency and highlights the need for autonomous maintenance is essential.
Short episodes of “Maintenance” from Taiichi Ohno have many things to consider.
Reference;
Nakajima, S. (1993, March). Plant Engineer JIPM, 25(4)(288), 46.
Takahashi, Y. (1997, July). Plant Engineer JIPM, 9(8)(100)), 32-37.