Structure and Dynamics
- hidet77
- Nov 16, 2021
- 5 min read
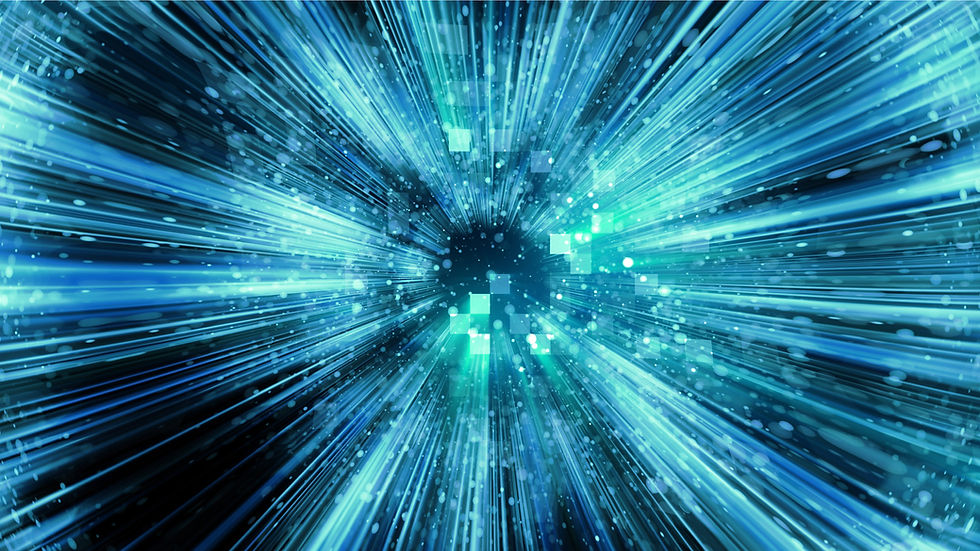
Why is the Toyota production system (TPS) difficult to understand?
In my last post, I talked about the change from Taylor to Toyota. As someone has already mentioned, why they made that change was because of necessity. But then, how did they come up with this idea? Culture? Leadership? Creativity? I won’t deny any of those, but there are some characteristics that I want to talk about.
Going to the shop floor with a TPS guru is an entertaining experience. You get to see live “think outside the box.” As I got to observe such opportunities, I started to recognize a pattern of their observations. They focus on “Structures” and “Dynamics.” “Structures” are not just organizations, which many start first and make mistakes. Their “Structures” begins at the process and breaking them into points – lines – areas, and body (organization). And then, they look at the “Dynamics.” Every shop floor, words, concepts, philosophies, and functions have “Structures” and “Dynamics.” By focusing on the simplest form of structure, they can re-structure them. In other words, they approached management as an engineer.
Suppose Taylor was the first one that mentioned the science of management. In that case, Toyota is the one who implemented the engineering of management.
This article is about the “Structures” and “Dynamics.” If you are interested, please take a look.
I mentioned that going to the shop floor with the TPS guru is entertaining. However, it was also painful at the beginning. The coach indicated many details. As one non-Toyota manager described, “TPS is about small things.” I thought so, too. I ran into this German proverb, “God dwells in the details,” and that justified my understandings. So, I became the annoying jerk who criticized every little thing.
Soon I was just stressed for both the shop floor and myself. Micromanagement is terrible for both sides. But because I felt that I was being micromanaged, I shouted within that “Why is this guy pointing small points after points after points?” That shout put me back to calm, and I decided to list those points he mentioned and mine.
An example of that list was the datum point. Once the coach pointed out the condition of a pin on a fixture. So, from that lesson, I pointed out the state of every pin. Later, the engineer told me that the pin that the coach challenged was the datum pin. It is crucial for quality. Then the engineer told me was that they recognized that some of the pins were excessive. So, instead of maintaining unnecessary pins, they reduced those. I was asking for unnecessary works. Thanks to this engineer, we found out the truth, and luckily, I did not push for unnecessary work. What I learned is that “God does not dwell in every detail. God dwells in the critical details.”
On the structure of “line,” flow is an important topic. TPS usually starts the plant tour from the shipping area. They observe how the product flows into the customer. After following the entire flow inside the factory, someone showed the value-stream map. The TPS guy looked at it and asked, “If the flow is this simple, why we don’t connect all the processes and make a large one-piece flow?” The author of the map responded that the processes are complicated. Therefore, we can’t make a sizeable one-piece flow. The TPS guy said, “Then write that complexity. Don’t make it simple just on paper.”
The thinking behind this TPS guy is essential. He is not just being annoying. He is purely an engineer. Suppose that there was a drawing of a product made by an engineer. The production guy came to the engineer and said, “Hey, I made something completely different from your drawing because it was too complicated.” What should the engineer do? Obviously, a more straightforward design is better, so the engineer must ensure the new simpler design meets the expectations. However, until the engineer changes the design, the production must not modify the product’s design. Production has come up with new creative, efficient designs, and engineers should be open-minded to such suggestions. However, an engineer can’t accept the gap between the drawings and reality.
The mindset that TPS people hate is the black-box thinking. They love the white box or the transparent box. They don’t like “somehow the material flows” or “somehow the volume of production was this” kind of explanations. They want to know the structure of the flow, volume, and everything. The unfortunate truth is that in business, this black-box thinking is quite convenient, like for cost accounting. Using the “Process costing” methods, we add all the costs and divide them by output to give the cost per unit. Then TPS asked, “I have a product that came straight from the line and another one that went to repair. Is the cost the same?” And then, they start diving into the box of process costing. Keeping a black box will not allow us to see the waste. We should hate the black box. And the truth about “Visualization” is that it is about the structure, not the numbers.
This mentality applies to other documents like standardized work or A3. These are the area of TPS structures. In Japanese, “Shiryou” means paperwork. But “Shi” could also mean death. In other words, dead work. What separates the paperwork and dead work is the dynamics on the shop floor. If everybody is following the standardized work, the dynamics will look synchronized and smooth. If not, that point that deviated is clear. Once this deviation happens, there should be dynamics to help and then solve the problem. It is always vital to synchronize the motion and heart (philosophy).
These structural and dynamic views apply to functions, such as quality, logistics, maintenance, etc. It is the function’s responsibility to realize into points – lines on the shop floor. This realization takes place in the form of work standards on top of standardized work. The team leader on the shop floor is responsible for making these detailed instructions on the topics of quality, skills, tools, TPM etc. But the functions must give directions on critical points and lines which the line can not compromise or violate. The functions can not issue a long list of things to do by the shop floor and walk away. That list and the work standard must integrate. Otherwise, the list will be ignored or become the additional cost of the shop floor.
After all, when I go to the shop floor, I always whisper “Point, Line, Area, Body” to understand it better. Once I know the structure, I start thinking about the value-add or waste. Otherwise, I might destroy the value-add work. For example, an inspection might look like a waste. But without a quality structure that is sufficient process control, taking an inspection out is suicidal. TPS is about the system formed by the points-lines-areas-body and the dynamics of those on the shop floor. During your observations of the shop floor, please try whispering “Points-lines-areas-body” and let me know what you discovered.
Comments