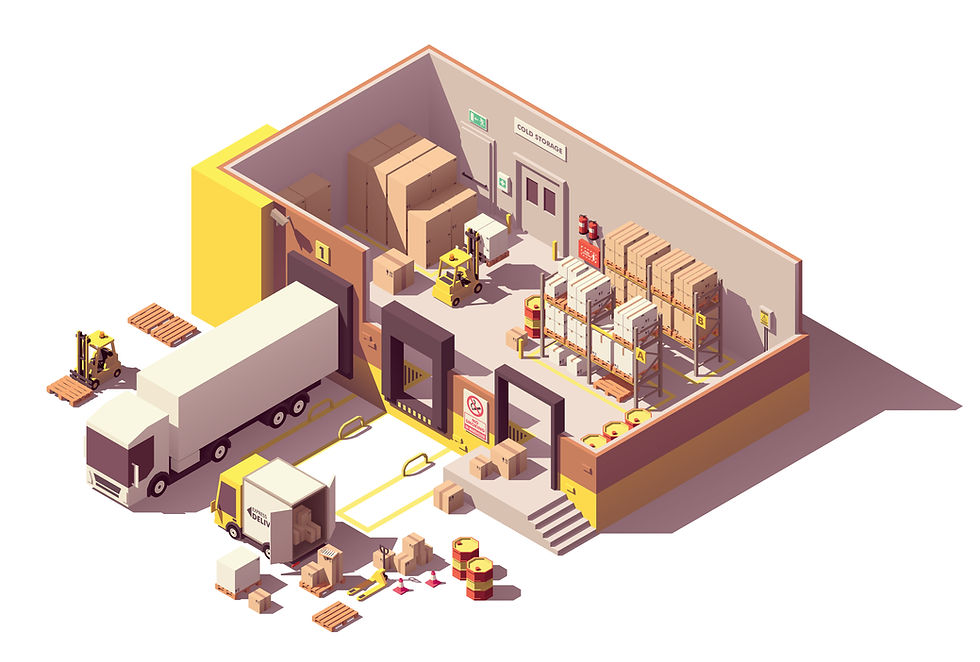
In my last post, I defended against critics for "Just In Time." Most of these critics end with a suggestion to increase inventory. I assume that they want to increase safety stock. This "religion" on safety stock is something I don't understand. I think there are excessive expectations on "safety stock." I will not start making a crazy statement like we should not keep safety stock. But we need to design "safety stock" properly. What is essential is safety flow, not safety stock.
Here is my statement.
1. Safety stock is not almighty protection. It is insurance. The more you want coverage, the more premium to pay.
1. Safety stock is not almighty protection. It is insurance. The more you want coverage, the more premium to pay.
The pandemic caused many supply chain turbulences. Due to these supply chain issues, many are asking for safety stock. Yes, we need some, but safety stock is not almighty. Safety stock is like insurance, and you decide what the insurance should cover, which will drive the premium. How much time do you want to cover? This pandemic is entering its third year. So, do we want to cover three years? It's easy to say, but that's a considerable premium. And anything below that level is just a random opinion. And how reasonable are these opinions? Let's be honest. The panic contributed to the current supply chain turbulences. I have already met many managers who confessed that they overreacted. This overreaction creates a bullwhip in the supply chain. The safety stock will not protect against overreaction or panic.
The supply chain will always have some kinds of disturbances. If somebody thinks that all problems will disappear by keeping some safety stock is a fantasy.
2. Safety stock is not going to make your process stable. Standardization will. What it is doing is reallocating time.
I often meet some people who recommend implementing a safety stock without visiting the shop floor to stabilize the process. Really? Is the safety stock going to make the process stable? I don't think so. It is a protection against the unstable process, and inconsistent process remains. It is a necessary part of operations. I am not going to eliminate all without approaching this topic logically. But I don't think implementing safety stock is as easy as many think.
Look at any calculations of safety stock. Those formulas require some assumptions on the lead time, volume, etc. It is excellent to calculate, but the gap between these assumptions and the reality of operating will kill the calculation. If the current condition is chaotic or not standardized, the baseline for such analysis does not exist. Some will argue that they are using historical data. Therefore, it should work. Unfortunately, historical data do not guarantee how we operate tomorrow. Standards will. Without standards, safety stock doesn't work. The standard should be the basis of any assumptions of calculation.
Back to the insurance analogy. Health insurance will not make someone healthier. Auto insurance will not make the car safer. We need to improve the process or the behavior.
3. What is critical during that time is the flow of recovery. Recover the safety stock. Recover from the crisis. Standardize these flows.
I was entering a factory on Monday morning. And this machine was down. Since we had two hours' worth of production as safety stock, it was okay for two hours. When all the safety stock was gone, now I was standing at the edge of a cliff. I started looking around for when or how are we going to refill. The next reliable time for recovery of safety stock is ... Sunday.
The critical part of safety stock is not about the quantity, which is the focus of the calculations. The crucial factor is the system of refill or the flow. A method of refill must exist separate from the regular flow. We often believe that we keep some extra capacity, such as the 80% loading rule, to refill the safety stock automatically. These expectations fail. Your processes were running at 80% and suddenly expecting to run at 100% to catch up is impossible. Factories running at 80% always have loopholes in their standards. Without closing those gaps, it is not possible to catch up.
This system of refill is not free and requires careful strategy. Without a plan, we wait for the refill of the safety stock, basically hoping that the subsequent process to go down. It sounds like an additional cost, but the truth is that the current system (non-TPS) is always hiding extra capacities. It is about surfacing those excess capacities and using them when the business needs them.
The system can either catch up or use overtime to refill the used safety stock. Both methods do cost more. Catch-up requires additional resources. Visualizing those additional resources is a must so that we don't hide capacity. Overtime is a headache, but safety stock should always be a headache for management. Otherwise, the problem will continue to stay inside an operation. Safety stock reallocates time. Good operations design shifts so that the responsible shift pays for the lost time. This creates a culture of responsibility. Many operate three shifts six days a week, which promotes irresponsible behaviors.
Back to the insurance analogy, again. Suppose that the insurance company did pay the claim. What happens next? Is the insurance company waiting for the excesses from the premium to load their cash? They probably have a diversified portfolio of assets that generate cash. They manage their assets so that they can handle future claims. The same thinking should exist in supply chain management. If the suppliers are in the same region, they have the same country or regional risks. Supply chain flow needs to be diversified and used in the Just In Time way.
4. Time is usually the enemy of problem-solving. Start the problem-solving immediately when someone touches the safety stock.
There is one truth about problem-solving. If you observe when a problem happens, it is easy to problem-solve. The more time has passed since the problem occurred, the more difficult it gets to problem solve.
Safety stock should not be in the way of problem-solving. There is this misunderstanding about what triggers problem-solving, and it is not when we run out of safety stock. If we start problem-solving when the safety stock runs out, you created this time, complicating problem-solving. Instead of attacking something fresh, you need to find out what happened in the past. The touch of safety stock must trigger problem-solving. Safety stock is insurance to protect the output, not an excuse for sabotaging problem-solving. Automobile accidents are investigated at the site immediately when they happen. Fire investigations take place immediately fire the fire is extinguished. And, you don't start the analysis of the problem when the insurance is paid.
So what will the conclusion of problem-solving be if it is done when we run out of safety stock? Simple. We need more safety stock. Many who are asking for more safety stock are making this mistake.
Don't become the victim of the insurance fraud called safety stock. You might be paying the premium for nothing.
Comments