Production "Management" Board
- hidet77
- Feb 18
- 4 min read

Production Analysis Board.
An essential tool that tracks the activities. Some might call it an “hour-by-hour” board.
I mentioned this before, but I do not like the term “Analysis” board. In Japanese, we call it a “production “Management (Kanri) board 【生産管理板】.” As we learn about this tool, we are repeatedly taught that it is not an analysis but a management tool.
When we say “management,” we refer to the PDCA cycle. In Japan, the other names for the PDCA cycle are the Deming circle or the management “Kanri” cycle. Although there are many opinions about the cycle, I will keep using it for simplicity's sake. The board should visualize the Plan, Do, Check, and Act Cycle, not just data collection and analysis. There is no value if this board doesn’t connect to some action.
To lead the board to the right action, the plan is crucial.
The plan is easy, right? We calculate the hourly target output and write it in each column. We should add one more column for accumulation, though the shift.
No. That’s too simple.
🔹 Time
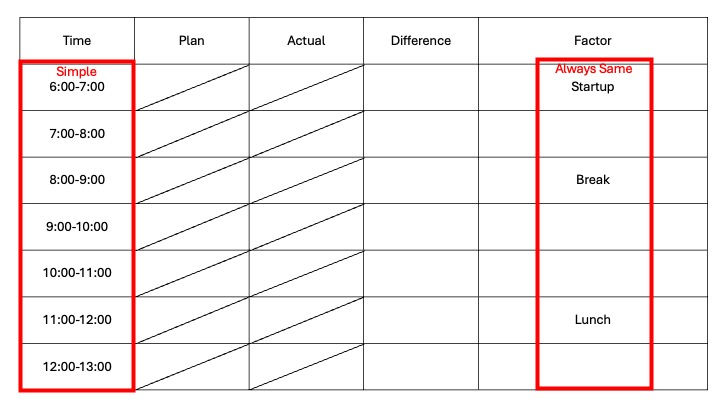
Many places write simple hours like 7:00 - 8:00. Since this is so “simple,” they always write "break, lunch, etc." in the remark section. Why do we always have to write the same thing again and again? This board should not be such a bureaucratic document. We all (should) know we go on breaks and lunches. Why don’t we plan those breaks and lunch times?
The more important question is why we can’t plan the breaks so that we always have a full one hour. As we investigate the logic behind deciding the breaks, we will face the truth: There is no logic. It is just how we have been doing it for a long time. I have been to a place where the first break was after one hour and 45 minutes of work, then 4 hours and 10 minutes to lunch. Did this make any sense? Instead of trying to survive in the illogic that was designed a long time ago, design good working hours. Typically, a two-hour increment is excellent. Write the exact start time on the board. In my previous post, I mentioned the “base unit.” What is the base unit of “Kanri” cycle? Set this as one-hour to make things simple.
🔹 Changeover
The changeover is a crucial moment in batch production. An unsuccessful changeover will cause delays, increased scrap, and potential injuries and damages to the machine and tooling. Management should pay attention to this moment. If so, highlight on the production “Kanri” board. In batch production, we don’t need the typical format with target numbers by hour. Instead, there should be a target time to complete the batch. I often hear that this is not easy. However, batch production should allow us to predict when they will complete a batch quickly. If not, that is not batch production.
🔹 Levelization
One important thing to note is that the planned target hourly output assumes a leveled workload. This is important because if there is no levelization and we just set the hourly output target, every negative number will be accompanied by the remark “high work contents.” Yet, we don’t know if we had such high work contents or not. We can’t validate if such remark was right or wrong.
I’m not trying to say that we need to perfect the levelization of the mix of work contents. However, we need to establish and follow some basic production patterns. Levelization is a subject of Kaizen, and that pattern should be sophisticated. But the idea here is to establish such a basic pattern as soon as possible so we can start avoiding writing the same reason, “high workload product,” again and gain. And, we should train the team leader to register what type of product they actually ran, which had high workload, so that they can plan production better. The Kaizen will stop when the “high workload” becomes the official excuse for negative output.
🔹 TQM & TPM activities
We must perform periodic quality checks and practice maintenance activities, which should be planned on the production “Management” board.
A factory conducted a quality check every 100 units of production. How did they do this? The inspector came at the end of the shift, looked at how much was produced, and then picked up consecutive units according to the ratio. This didn’t seem like good sampling to me. So I created slots next to the production “management” board where I wrote down what time the unit was ready to be inspected. This outraged the inspectors. Why? Because this took away their freedom to go to smoking other important activities. I’m sorry, but I want to make things easy, not lazy.
A machine required frequent tooling changes. The team used to mix up the tooling or forget to change it at the right time, producing many defects. We created tooling slots on the production “management” board to avoid this mess. As the team leader planned the day, preparing all the tooling for the shift became part of his planning. According to the production schedule, they placed the tooling in the right slot. This simplified tooling changes. There was no need to search for or mix the wrong tool.
These TQM and TPM activities are critical for the success of production. Make them visible on the production “management” board so you don’t forget them and can take action.
Please don’t think the Production “Management” board is just for data collection. It has far more uses. The most important thing is to take action, starting with good planning.
Comments