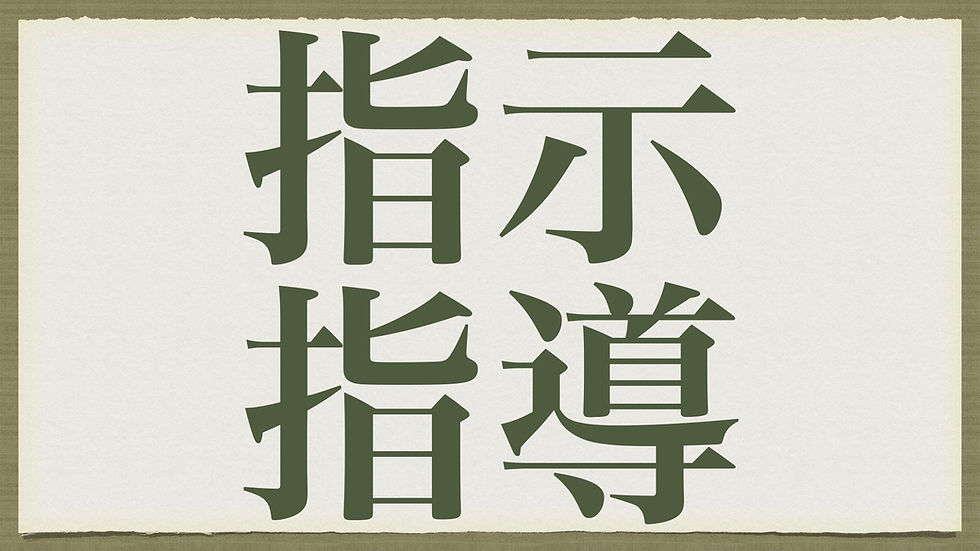
This word is used at least twice in the Toyota Production System.
1️⃣ Production “Instruction” Kanban
2️⃣ Job (or Work) “Instruction” Sheet
What are your impressions of the word “Instruction”? Is it the same or different? It should be different because TPS uses two other Japanese words.
1️⃣ Production Instruction Kanban
Production instruction Kanban is a tool that provides permission to start production activity. (Broad meaning) The form or shape could change according to the type of process. The assembly line will point this production instruction Kanban in front of the product to inform the specific product that needs to be produced. Batch production will use Signal (or trigger) Kanban to start a batch.
The Japanese word used for “instruction” is Shiji【指示】. The first symbol 【指】 is a finger. The second symbol means to show or direct. The word comes from someone pointing the finger in the direction. A different way of translating this word will be “order.”
There is a similar word in Japanese, Sashizu【指図】. This is pointing to a Zu, which means a figure or drawing. This word appears from the Eighth century in Japan. I wonder what kind of drawings there were at such a time. The meaning is similar to Shiji. I imagine a situation in which a boss gives instructions on constructing something using some kind of drawing.
2️⃣ Job (or Work) Instruction Sheet
Job (or Work) Instruction Sheet is one of the work standard documents used to train someone. This provides the instructions we must give the trainee at each process step.
The Japanese word for this “instruction” is Shidou【指導】. The second symbol, Dou【導】, has the way【道】 on the top and the form of a finger【寸】 on the bottom. This symbol means to guide or navigate. Therefore, Shidou means to coach or guide. Shidou also means to lead. We mixed leading and coaching. The job instruction sheet is designed to coach someone on the skills required to perform the work. It should highlight the critical points that should be followed. However, some questions from the trainee are always welcomed and used to improve the “instruction.”
Interestingly, some of Japan's old job instruction sheets were called Sashizu documents. For example, Inoue shows a work instruction sheet that uses the word “Sashizu” in his book “Scientific Management for Engineers (1927).”
So what is the difference between “Shiji/Sashizu” and “Shidou?”
In general, Shiji【指示】 has more binding authority than Shidou【指導】. This is the case in government “instructions.” When the government uses the word Shiji, it has less binding power than words like “warning” but more than Shidou. Shidou will have more choices than Shiji.
Why is this distinction important?
Because in typical operations, the relationship between the two “instructions” is opposite.
First, “instructions” are not followed in many places, creating chaotic conditions. In such a case, we should not use the word “instruction” since there are none. An ignored instruction is the same as nothing.
However, the typical problem is that there is more freedom to change the production instructions and commands regarding the job instructions.
There was a factory with a “Bad shift.” As we investigated, we found out that so-called “Good” shifts changed the production instructions and selected to produce only easy units. Once we made sure that all shifts followed the production instructions, we learned that there was no such thing as “good” or “bad” shifts. The more significant issue was that management only checked the output, not what was inside that volume. This phenomenon of giving freedom not to follow the production instructions is prominent in many places. Workers are somewhat expected to ignore the schedule based on material availability. Production plans are expected not to be followed. But that hides the problem of materials that did not arrive on time. Again, management checks the output only, which is outdated in today’s high-mix product lineups.
There are many places where people do not follow the standards. Instead of just pushing people to follow, picking up one of those standards and checking at the Genba is also good. Many of those standards are unfollowable. Pushing people to follow something that will create a negative outcome is wrong. At the same time, not following since it is not perfect is also silly. This is why we need to use Kaizen. We start with a standard; if something goes wrong, we just improve it. Use the job instruction sheet to guide the people in the right direction. If incorrect, just improve it.
What does “instruction” mean to your organization? What “power” does it possess? Are we giving the right power to the right “instruction”?
Comments