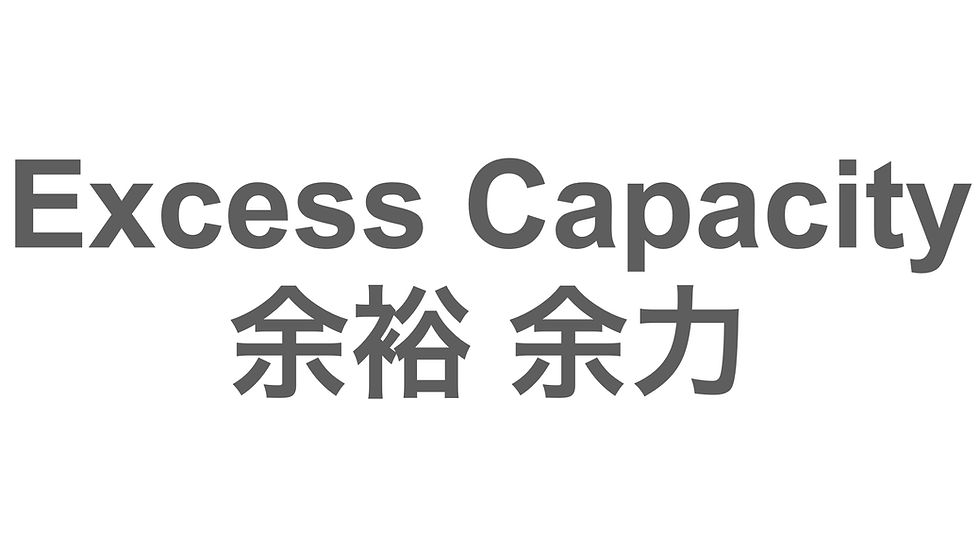
Generate "Excess capacity"???
In Ohno’s “Toyota Production System,” there is a chapter called “Generate Excess Capacity.” This is not wrong thinking. Toyota has been serious about this philosophy since they again put it in Toyota Way 2020.
It is a weird chapter since the system is about waste elimination. Isn’t excess capacity a waste?
Toyota keeps using the word “Yoryoku (余力),” not “Yoyuu (余裕),” which both can be translated as “Excess capacity.” There is a slight difference in the nuances of the words.
And it is crucial to keep this “Yoryoku (余力),” but in what form? And who should be responsible and how?
In the Toyota Way 2020, there is a phrase called “Create “Yoryoku (余力).” It comes from Ohno’s “Toyota Production System,” “Generate Excess Capacity.”
When we Japanese use the word “Yoryoku (余力),” we always touch it twin “Yoyuu (余裕).”
“Yoryoku (余力)” = excess power left AFTER you did work.
“Yoyuu (余裕)” = to PLAN something more than necessary. Or less than a limit. Piece of mind.
If we try to translate those words, those would be;
“Yoryoku (余力)” = Remaining power, Reserve force
“Yoyuu (余裕)” = Allowances, Additional coverage, Time (to spare), room, a margin
These translations highlight the differences inside the “Excess capacity.”
The first difference is before and after the work.
Ohno & Toyota is trying to make “Extra capacity” after the work is done. This means that this “Extra capacity” is made through Kaizen. This is the reason why Ohno used the word “Generate” before the word “Yoryoku (余力),” while Toyota Way 2020 used the word “Create.”
On the other hand, “Yoyuu (余裕)” is something done before the work. Yet, it needs to be careful. “Excess capacity” could generate a sense of negligence and carelessness.
This connects the second difference. In what form the “Excess capacity” is kept?
In “Yoyuu (余裕),” we keep these in numbers or ratios. For example, somehow giving cycle work 20% below Takt time. 80% OEE. The safety ratio on included in the Kanban calculation. As a result, these numbers and ratios hide problems. It makes the line between standard and problem very vague. Abnormal becomes normal.
On the other hand, “Yoryoku (余力)” should be kept as a resource. The team leader responds to Andon pull due to fluctuations. Safety stock. Time allocated for overtime. These resources are kept “free” so that if something happens, the resource will be deployed. It is clear to anyone that an “extra” resource has been used. Therefore, it is recognized as a “Problem.” As we Kaizen, “Yoryoku (余力)” in the form of a resource will be taken out and kept as “Yoyuu (余裕)” in the system.
The third difference is that this “Excess capacity” is in a manager's hands.
I have been to many factories claiming they are “full capacity.” But the truth is that much “excess capacity” is hidden in the processes. But those “excess capacity” is not under management. For example, OEE 80% rule. 20% planned downtime vs. unplanned downtime is two completely different worlds. When you have 20% unplanned downtimes, 20% can’t be used for other purposes. The manager doesn’t know when and why those downtimes will happen, so it can’t touch. It is like gambling, and the odds are that you lose a day of production in a week. On the other hand, planned downtime is under management. Why and when is clear. Then, by focusing on those reasons, a manager can generate “Yoryoku (余力).” The best example I always use is Shogi.
The fourth and perhaps most important issue is the trust.
Business can’t exist without some “Excess capacity.” “Full capacity” is a fake. But do I want to expose that “Excess capacity” or play a “hide-and-seek” depends on the trust. As I found many hidden capacities, I also met managers who scolded those who hid. But the reason why people hide excess capacity is because of the manager itself. The manager will blame the people when there is a problem. Since people don’t know what kind of problem they will face in the future, they do their best to “hide” excess capacities. They are often blamed for something entirely out of their control. On the other hand, places where people are open about their “excess capacity” is where managers don’t blame people for the problem. First, the managers blame themselves for not seeing the “excess capacity” or the problem. Then they thank people for highlighting a problem. Ultimately, although people are involved and encouraged to problem-solve, the manager is responsible for problem-solving. Since the people trust that the manager will care for the problems, they give away their “excess capacities.”
In the end, both “Yoryoku (余力)” and “Yoyuu (余裕)” exist in the operations or business. The success depends on how you manage those.
コメント