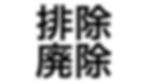
Taiichi Ohno and the Toyota Production System sometimes use “old” Japanese, which we must be careful of. One such example is the word “wisdom.” Understanding the insights of the “old” words can give us hints to improve.
Ohno commented on eliminating Muda (Waste) in some old interviews.
“We need to eliminate “Haizyo”【廃除】 Muda (Waste), not eliminate “Haizyo” 【排除】.”
🤔🤔🤯
Both “eliminate” were pronounced as “Haizyo," but he wrote two symbols for the word.
The typical word for “Haizyo” is 【排除】. That is how modern Japanese teaches it. The older version that Ohno used was 【廃除】. Let’s take a deeper look at the difference between these.
The first version 【排】has the shape of a hand on the left side. The right side represents something coming out of the gate, which means this symbol represents pushing unnecessary things out of the gate.
The second version【廃】 has the shape of the house on the top. The bottom part was initially meant as an enemy, which was shaped like a bow and soldier. Therefore, it meant the demolished house by the enemy. From that, the symbol represents decline or stop the use. Today, this version of “Haizyo” is only used in Law, which is used to abolish inheritance. I guess that this word was used from the Samurai days, and even if we try to simplify it today, our culture couldn’t stop using this symbol for this purpose.
Another way to look at this is;
Body waste is described as 【排泄物】.
The waste or garbage is described as 【廃棄物】.
The first is because we are pushing waste out of our bodies. The second is that we are completely eliminating the garbage.
Back to Ohno’s quote, he warns us that eliminating means completely disappearing the specific Muda from anywhere. It is not about pushing the waste out of the process.
A classic example is moving the waste to the subassembly. I have encountered many cases where they wanted to move the subassembly out. Then, they claim they have improved the process since the cycle time has decreased by ignoring the subassembly processes. They argue, “Our process is in better shape; therefore, this is good.” But what about the subassembly? The critical question is whether there has been any change in total productivity. Partial optimization doesn’t save any cost for the business; instead, it could damage them. A similar example is outsourcing. The cost might go down. But that doesn’t mean the productivity will change. We need to make sure why the price of the outsourced supplier is cheaper. In many cases, they sacrifice something important like quality, costing more at the market. At least, outsourcing is a business decision, not Kaizen.
Another example of moving waste is automation. When we questioned the human's motion, some proposed using a robot. Since the robot moves faster, they claimed that it improves. But the truth is the robot is doing a wasted motion. We just moved waste from humans to robots. A similar kind of pushing waste to machinery is transportation. Transportation machinery has more power to move faster and lift things. But does that justify them for doing excessive lifting and moving around? I heard a story of a part that traveled around the world three times to reach the customer. Just because machines can do faster, the waste is still a waste. If someone else can do it in another way without the waste, their cost structure will threaten you.
Be careful with pushing the waste out. It might be out of a process, group, department, factory, or business. But if we haven’t eliminated it, the waste is still there and comes back at you differently. Most likely, you just converted the accounts from one to another. This is not Kaizen.
(Applogies for dirty examples.)