Brief history of 5S in Japanese Factories
- hidet77
- Jan 16, 2024
- 4 min read
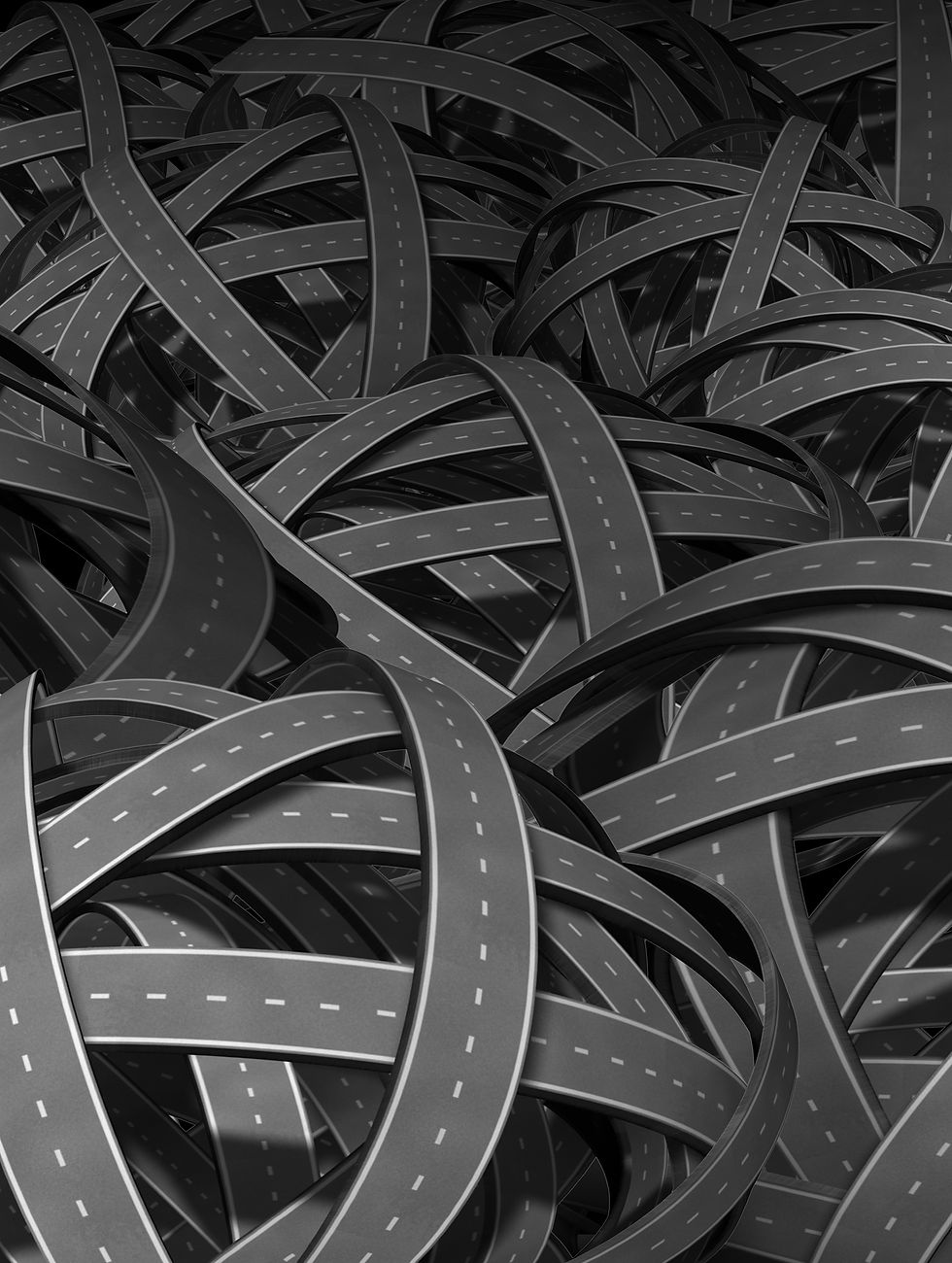
This post is about a brief history of 5S in Japanese factories.
This will ignore some philosophical aspects or activities outside manufacturing.
Understanding history will guide us to better thinking. The truth is that 5S has many roots with different philosophies. Just because they use the exact words doesn’t mean the philosophies are identical.
1️⃣ Early days: independent “S” activities.
Japan faced a dilemma as it modernized and started introducing modern factories in the late 19th century. The employee morale was low. The discipline was poor. They smoked. Some peed on the floor.😱 Muds and dirt were everywhere on the floor. Factories were suffering with diligence (I’m sure I destroyed some images of Japanese).
To overcome such issues, new initiatives were taken. The employees were asked to clean the factory. As things got cleaner, the morale went up. Nobody will pee on the floor when they know they have cleaned it later. People like Araki promoted such activities. It was more economical than hiring more cleaning staff. These were the early phases of all employee participation movement. Another critical point was that the early days of “Scientific management” in Japan were led by Ueno, a psychologist who thought about employee mental health. Organized conditions were better for mental health and efficiency.
As these activities became more popular, we started seeing more events— like “Seisou” day or “Seiton” day. And we start to see combinations like “Seisou-Seiri” week. By the way, I can say that although we use the exact words, the meanings are slightly different. For example, in most cases, “Seiton” means to throw away unnecessary things. These activities were tied to “waste elimination【無駄省き; Muda Habuki】” and cost savings【節約; Setsuyaku】 way before Ohno started the TPS. Note here that I introduced another Japanese “S” word, “Setsuyaku,” but never in the part of 5S or whatever Ss. There is a simple rule. Cost savings are the objective, not the method. We should be distinguishing the two, please.
Another important initiative is that thinking of “Public health” proliferated in Japan around the same time. This thinking led to “Seiketsu” to keep everything clean. By connecting new thinking with something we already have, the Japanese proliferate the concept fast.
2️⃣ Safety improvement activity called 3S
As we entered the 20th century, another topic became hot in Japan.
Safety.
In mid-1910, Japan lost 6000 workers inside factories in a single year. This was unacceptable.
So, the Japanese started the “Safety First” activity by gaining influence from the example of US Steel. US Steel started the “Safety First, Quality Second, Productivity Third” initiative in the early 1900s. This movement reached Japan in the mid-1910. This movement started to connect other “S” activities. They started to call “Seiri,” “Seiton,” and “Seisou” as 3S and became the basics of safety. The 3S (Eventually 4S) became a massive movement to improve safety.
One important lesson the Japanese learned from US steel was that “Factory layout, machine allocation should be in sequence to avoid materials getting “tangled.” Early thought on a layout based on the work sequence is here.
In Toyota, like many other Japanese companies, “3S” or “4S” first appears in the safety movement. 4S was introduced to improve safety. According to Toyota’s 75-year history, the 4S movement in Toyota started in 1961 as a safety improvement initiative. Their impact is on this graph.
So why safety is not part of 5S? Again, safety was the number one objective of introducing 4S. One is objective, and the others are methods. Let’s not mix them.
3️⃣ What are the uniqueness of 5S in TPS?
And TPS shifted the meaning from safety to a unique way. The uniqueness of 5S in TPS is that they have standardized work at the core.
Implementation of standardized work started in the late 40s to early 50s. Standardized work focuses on human work and its movements. Core thinking is that machine layout and material locations should follow the most efficient human work. It is not the other way around, which I have seen many behind the so-called “5S.” Also, in creating a standardized work, there is a step called “Work Seiri,” in which we must ensure that safety (and other things) is respected. “Time study” comes after such a step.
One crucial change behind the standardized work is that the meaning of waste has changed. Taiichi Ohno introduced “Over-production.” To control over-production, takt time was used to balance the work among processes. The meaning of 5S before and after defining over-production is entirely different. When over-production is recognized as waste, 5S is a powerful tool to prevent and highlight the over-production. Yet, when over-production is not recognized as waste or promoted in many cases, 5S must be some dead-stock cleaning activity. None of the 5S words are unique to TPS. “Muda (Waste)” is also used way before TPS. Yet, standardized work and over-production change the meaning.
All 5S words are very common Japanese words used inside factories for decades. Common; therefore, it functions as a slogan but has many interpretations. 5S has many roots, even from outside Japan. Understanding the background or the history helps us understand the meaning better.
References;
Hiroyoshi Takagi, “5S 活 動 の 生 成 と 展 開” 経営論集 第16巻第1号 2006年 127~143頁
Shin Ohmori, “日本企業と掃除 5S活動生成と展開の歴史と手段重視型の経営” 日本経営学会誌 第 42号, p p.27-39, 2019
Comments